Быть экологически ответственнным
Итальянская отделочная фабрика Mascioni всегда фокусировалась на трех ключевых понятиях: качество, инновации и уважение к окружающей среде.
Менеджер по продажам Марчелло Морбелло вместе с менеджером по производству Эжидио Фазана рассказывают об огромных усилиях компании в отношении фильтрации сточных вод от веществ, появляющихся в результате процесса покраски и печати.
Кювио - небольшая коммуна в североитальянской области Ломбардия, расположенная совсем недалеко от озера Лаго-Маджоре. Компания Mascioni S.p.a. является одной из крупнейших отделочных фабрик в Европе и находится в этом живописном регионе с 1950-х годов. Она производит домашний текстиль для таких брендов, как Basetti, Armani, Missioni, Calvin Klein, Ralph Lauren и Zara, а также гостиничный и технический текстиль. Вместе с одеждой всё это создается на владениях компании общей площадью 430000 кв. м.
Оптимальной отделки можно добиться разными способами, в зависимости от ткани. В дополнение к механической и термальной обработке используется длинный список химикатов. Обеспокоенность расположением фабрики в местах с идиллическими пейзажами не является чем-то новым для Марчелло Морбелло - менеджера по продажам: "Любой производитель в этом регионе знает, что устойчивость - не просто фраза, используемая в маркетинге".
Поскольку экологическая ответственность и экономическая деятельность идут рука об руку, Mascioni управляет одним из наиболее прогрессивных производств во всем мире. И тем не менее, процесс отделки 35 миллионов метров в год требует значительного количества воды: "Один килограмм текстиля потребляет около 190 литров воды, или, другими словами, на один метр нужно потратить 57 литров", - поясняет Эжидио Фазана, менеджер по производству. Эта сточная вода должна быть обработана перед тем как сможет снова использоваться в производственном цикле или будет возвращена в окружающую среду.
В 1971, задолго до того как итальянское правительство закрепило всё на законодательном уровне, Mascioni установили свою собственную очистную установку. Она постоянно обновлялась в течение многих лет. Поэтому сегодня сооружение способно устранять множество вредных веществ, являющихся результатом различных стадий процесса отделки.
На первом этапе очистки из полученной ткани удаляются любые следы пропитки и других остатков. Последние включают в себя смолистые вещества, полиакриловую кислоту, поливинилалкоголь, а также карбоксиметилцеллюлозу, повышающую устойчивость нитей к растяжению в процессе прядения. Также нужно избавиться от любых остатков жира, масла или воска, появляющихся в процессе производства волокон, перед началом окрашивания и печати. В зависимости от термостойкости материала, для этого при высокой температуре добавляют гидроксид натрия, карбонат натрия, очищающие агенты и эмульгаторы.
Чтобы ликвидировать характерное для натуральных волокон желтое обесцвечивание, на втором этапе нужны окисляющие вещества, например, соединения хлора и пербораты, часто используемые вместе с фосфатами и поверхностно-активными веществами. Только затем можно приступить к покраске и печати. Здесь ПАВы требуются для гарантии того, что красители равномерно и полностью проникнут в волокна. Качество хлопка можно особенно улучшить мерсеризацией: концентрированный раствор едкого натра придает материалу шелковый, стойкий к стиркам блеск, больший удельный вес, улучшенные показатели предела прочности и эластичности, а также дольше сохраняет первоначальный тон. После высыхания краски поверхность обрабатывают специальными смолами или неорганическими веществами. Они помогают предотвратить появление складок на ткани или сделать ее водонепроницаемой или антибактериальной.
Между этапами отделки материал нужно полоскать и сушить, чтобы удалить химикаты или остатки краски. "Нам требуется около двух миллионов кубометров воды в год", - объясняет Фазана. Этого объема хватит, чтобы заполнить 800 олимпийских бассейнов. Вода берется из 10 подземных источников, расположенных под владениями компании, некоторые из которых имеют глубину 70 метров. "Эта местность раньше была болотом, сейчас же - богатый источник воды", - говорит Фазана.
Сложный коктейль из химикатов, остающихся после производства, распадается на безвредные субстанции в процессе детальной биологической обработки. Необходимые для этого резервуары покрывают площадь в 40000 кв. м., что эквивалентно пяти футбольным полям. Итак, на следующем этапе вода временно размещается в двух разных баках, один из которых способен вобрать в себя до 12000 кубометров и хранит очень сильно загрязненную воду, полученную после полоскания, отбеливания и покраски, а другой - промежуточный - имеет объем 16000 кубометров и хранит менее загрязненную воду.
Эти два бака гарантируют, что перед началом биологической очистки вода будет иметь равномерное распределение вредных веществ. На этом этапе микроорганизмы разлагают загрязнители, содержащиеся в так называемом активном иле. Результатом этого процесса являются безопасные химические соединения. Следующая стадия - отстойник, в котором ил и вода разделяются. После такой обработки воду можно снова использовать в производстве или можно вернуть ее в окружающую среду.
"В своей пятидесятилетней истории Mascioni всегда инвестировали в новые технологии и инновации с целью разработки более эффективных и ресурсосберегающих способов производства", - объясняет Морбелло. Самые последние инновации мира текстильной печати - это цифровые технологии. "По сравнению с производителями из региона Комо мы поздно вошли в цифровое производство, однако мы не работаем с ограниченным количеством дорогих материалов (например, шелком) - мы обрабатываем большие объемы хлопка и льна. Поэтому клиентов заботит не только качество, но также скорость работы и выгодные условия", - заявляет менеджер по продажам Mascioni. В течение долгого времени просто не существовало цифрового решения, удовлетворяющего всем критериям.
Поскольку ключевой бизнес Mascioni - это производство домашнего текстиля с шириной до 280 сантиметров, никакие из доступных ранее систем не отвечали требованиям в отношении ширины печати, качества печати и скорости работы. Kappa 180, первый из высокоскоростных струйных принтеров Durst, представленный на международной выставке текстильных машин ITMA 2011, оказался наиболее подходящим кандидатом. К сожалению, максимальная ширина была 195 см, поэтому Durst и Mascioni решили скооперироваться и начали разработку принтера Kappa 320 с максимальной шириной печати 330 см и гарантированным качеством 1000 dpi, а также скоростью до 900 кв. м. в час. Поскольку он оборудован по технологии печатных голов Durst V2, в которой цвета располагаются симметрично в восьмиканальных печатных модулях, Kappa 320 обеспечивает абсолютное соответствие цветов при двунаправленном режиме печати. Вдобавок к дисперсионным и кислотным чернилам также доступна GOTS-сертифицированная система реактивных чернил, позволяющая печатать на шелке и полиамиде. На сегодняшний день Mascioni производит 30000 метров в неделю с помощью трех печатных комплексов Durst Kappa.
Цифровая печать не только предоставляет новые рыночные возможности, она также дает, в сравнении с обычными способами печати, много преимуществ. Недавние исследования показали, что цифровые технологии сокращают потребление энергии на 30-50% и воды на 75-90%. Главная причина этого - менее интенсивная очистка машин, барабанов и шаблонов.
Другим фактором являются более экологически безопасные чернила. "Мы постоянно стремимся сократить воздействие индустрии текстильной отделки на окружающую среду", - уверяет Фазана. Это становится всё более и более необходимым, потому что глобальный рынок смотрит не только на качество продуктов. Он также рассматривает влияние производства на общественное здоровье и окружающую среду. В этом отношении компания Mascioni определенно хорошо подготовлена к будущему.
Перевод статьи "Verantwortung mit Weitsicht" из журнала Durst Surfaces 01/2015.
http://www.durst.it/en/index.php/site/surfaces
Связанные продукты
Рекомендованные статьи
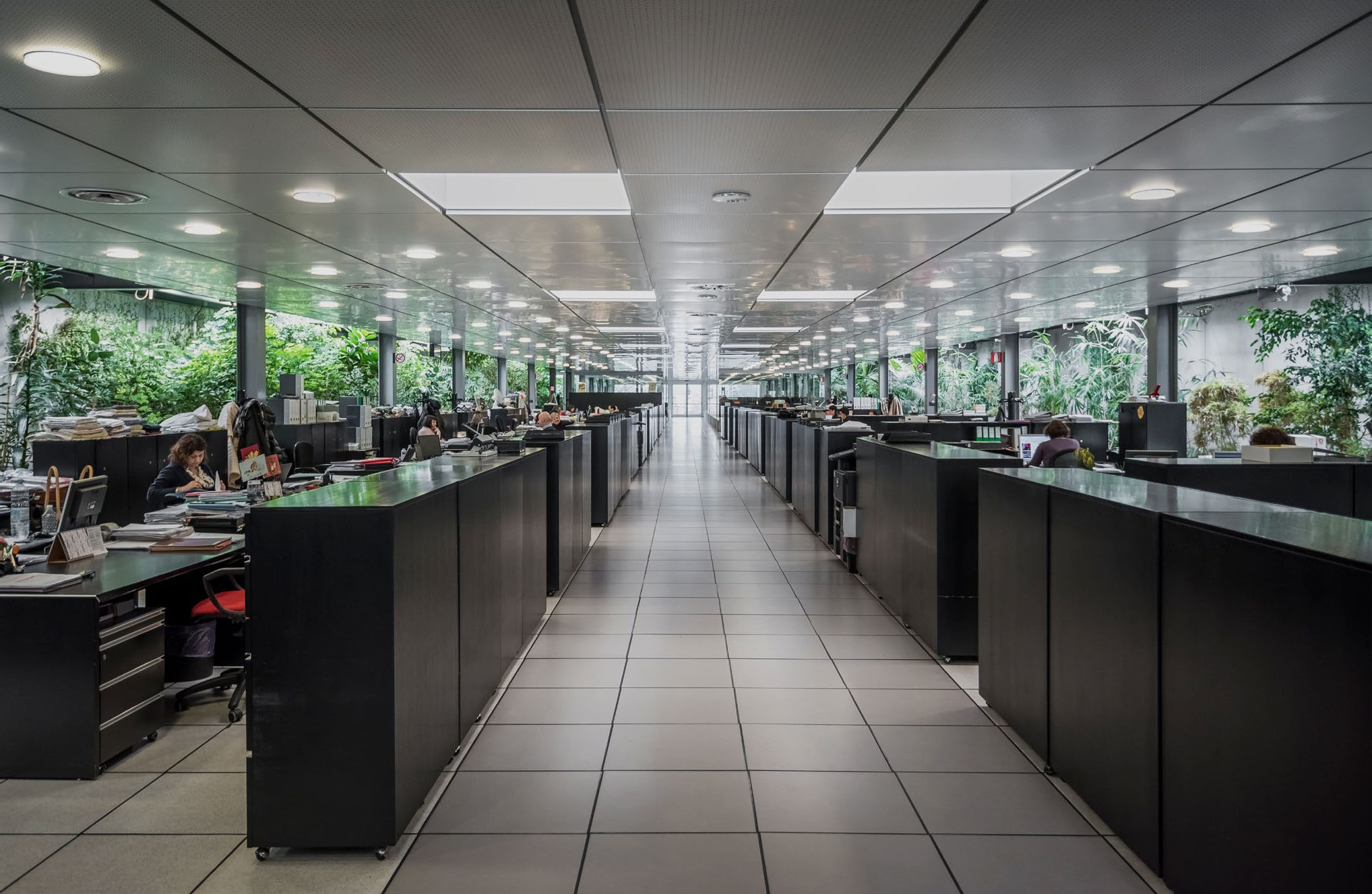

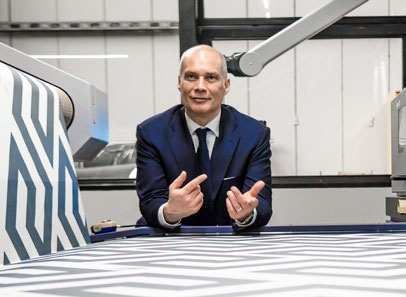
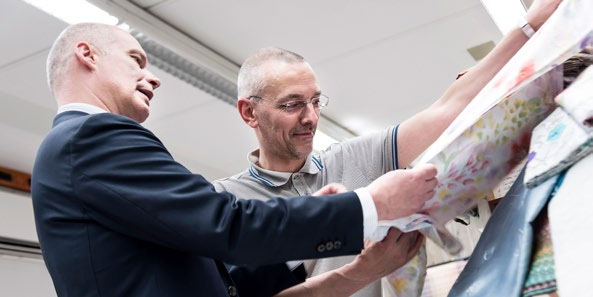
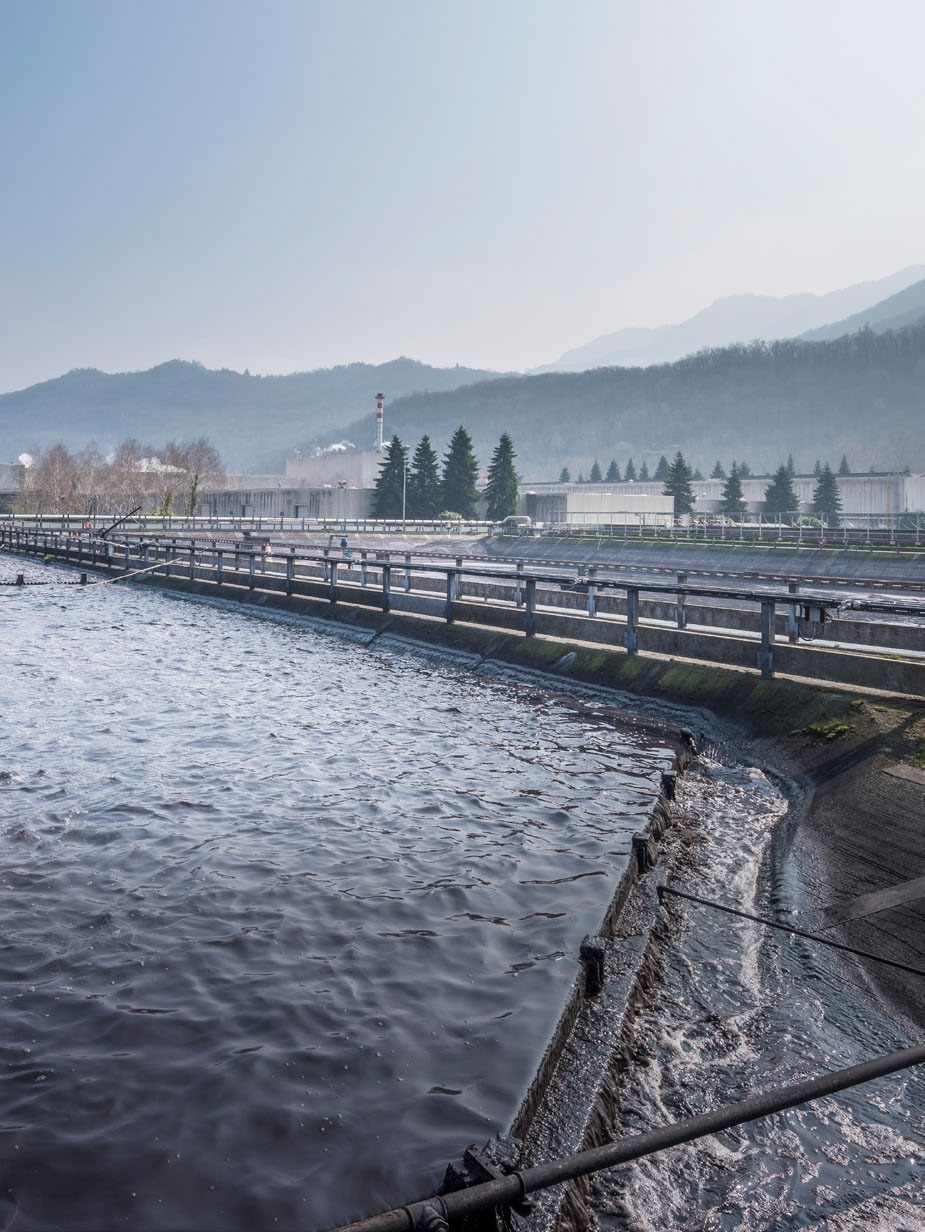
